A Behind-the-Scenes Look at Distribution Transformer Manufacturing Processes
Distribution transformers are vital for stepping down energy from high-voltage transmission lines to levels suitable for end users. Their critical role in maintaining reliable energy flow makes them indispensable for industrial and commercial operations. However, crafting these transformers requires a combination of technical precision, advanced materials, and meticulous processes.
Producing high-performance transformers is no simple task. It demands expertise and attention to detail at every stage, from initial design to final delivery. Partnering with a trusted distribution transformer manufacturing solutions specialist, like JCL Energy, provides access to products that meet the highest standards of quality and performance.
#Step 1: Design and Specifications
The foundation of any high-quality distribution transformer manufacturing process begins with precise design and specifications. This stage emphasizes collaboration between the provider and client to make sure that the product meets exact operational requirements while adhering to industry standards and certifications.
Key steps in this distribution transformer manufacturing process include:
- Defining Requirements: Gathering operational specifications from the client.
- Custom Transformer Specifications: For specialized requirements, such as electrical distribution transformers, tailored solutions are developed to meet specific application needs upon request.
- Meeting Compliance: Verifying adherence to industry standards for safety and reliability.
- Optimizing Performance: Engineering for reliability and durability in demanding environments.
By focusing on these elements, providers like JCL Energy deliver units that integrate easily into energy systems while addressing modern power challenges.
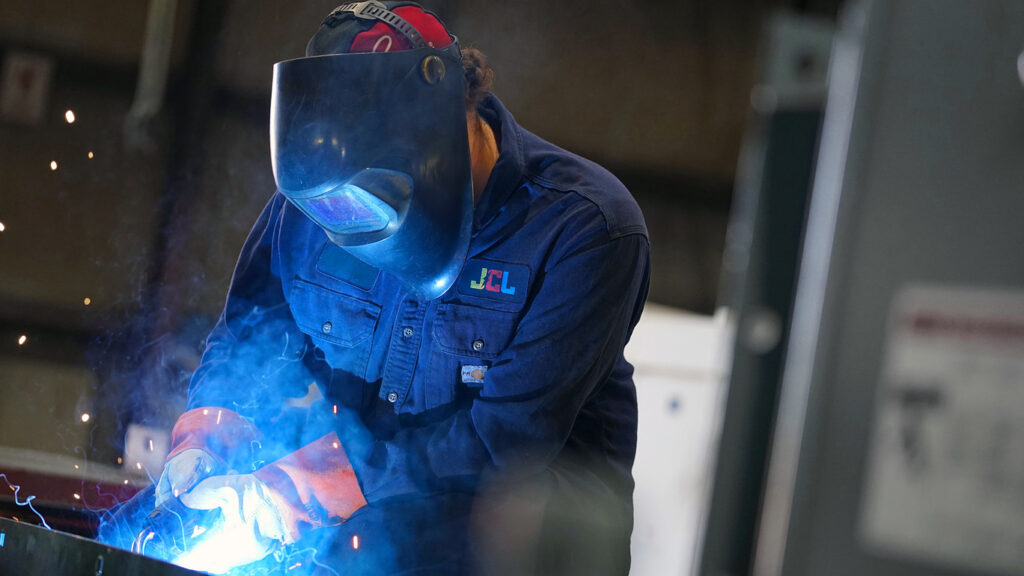
#Step 2: Material Selection and Procurement
Once the design is finalized, the next step in distribution transformer manufacturing involves selecting and procuring high-quality materials. Manufacturing providers focus on sourcing premium materials for the following components:
- Cores: Magnetic cores made from grain-oriented or amorphous steel minimize energy losses, enhancing overall efficiency. These materials are important for reducing core losses in transformers, especially those used in high-demand environments.
- Windings: Copper or aluminum windings with low electrical resistance provide optimal conductivity while reducing heat generation. The choice of winding material depends on the specific application and cost considerations.
- Insulation: High-grade insulation materials, such as epoxy resin for dry-type transformers or oil-based insulation for padmounted transformers, protect against electrical faults and environmental stress.
- Casings: Durable enclosures made from weather-resistant steel or aluminum safeguard internal components from external factors like moisture, debris, and temperature fluctuations.
#Step 3: Core Assembly and Winding
After sourcing high-quality materials, the next phase in distribution transformer manufacturing is the precise assembly of the core and windings. This step is vital to the transformer’s energy efficiency and operational performance and requires technical expertise and attention to detail.
- Core Lamination Process: The core is built using thin sheets of grain-oriented steel, meticulously layered to reduce eddy current losses. Each lamination minimizes magnetic resistance, optimizing the transformer’s ability to transfer energy efficiently. This process is particularly important for applications involving substation transformers, where high-voltage systems demand superior magnetic performance to maintain consistent power distribution.
- Winding Techniques: The winding process involves wrapping copper or aluminum conductors around the core in precise patterns. The configuration of these windings, whether circular, helical, or interleaved, depends on the transformer’s load and voltage requirements. Proper spacing and alignment are critical to minimizing resistance and reducing heat generation during operation.
By carefully balancing core assembly and winding precision, distribution transformer manufacturing providers can deliver reliable performance while minimizing losses in demanding industrial and commercial applications.
#Step 4: Insulation and Cooling Systems
With the core and windings assembled, the next phase in distribution transformer manufacturing focuses on insulation and cooling systems. These components are critical for maintaining performance, preventing faults, and long-term reliability in different transformer types.
Insulation Methods Across Transformer Types
- Padmount Transformers: For outdoor installations, robust insulation materials protect against environmental factors like moisture, dust, and debris. High-dielectric oil-based insulation not only prevents electrical faults but also extends operational life in harsh conditions.
- Dry-Type Transformers: Resin or varnish-based insulation provides fire-resistant protection, making these transformers ideal for indoor or confined spaces. This method enhances durability and safeguards systems in environments where liquid insulation is not feasible.
- Substation Transformers: Advanced insulation techniques are crucial for managing the high voltages required in substation applications. These methods provide superior protection against electrical stress, providing safety and uninterrupted performance in critical power systems.
Cooling Systems Tailored to Transformer Types
- Oil-Immersed Cooling for Padmounts and Substations: These systems use insulating oil as both a coolant and a medium for heat dissipation. The oil absorbs excess heat generated during operation and circulates to maintain optimal temperatures, supporting long-term reliability in high-demand applications.
- Air-Cooled Systems for Dry-Types: Natural air circulation or forced air cooling manages heat effectively without the use of liquids. These systems are used for dry-type transformers, offering efficient thermal management in applications where liquid cooling is impractical.
By tailoring these systems to the specific needs of industrial transformers, these products can operate efficiently and withstand demanding conditions.
#Step 5: Testing and Quality Control
Once the insulation and cooling systems are integrated, the next stage in distribution transformer manufacturing is rigorous testing and quality control. This process validates the performance, safety, and compliance of the finished transformers, making sure they meet the demanding requirements of industrial and commercial energy systems.
Comprehensive Testing to Validate Performance
- Efficiency and Load Tests: These tests evaluate how well the transformer performs under various load conditions. By simulating real-world operating scenarios, manufacturers identify potential inefficiencies and optimize energy transfer for maximum performance.
- Safety Tests: Dielectric strength tests assess the transformer’s ability to withstand electrical stress, while short circuit tests simulate high-current scenarios to confirm operational safety. These evaluations are critical for high-voltage systems like custom transformers, where reliability is non-negotiable.
Beyond testing, quality control processes are implemented at every stage of the distribution transformer manufacturing production to uphold high standards. From inspecting materials to verifying assembly precision, each step is scrutinized to prevent defects and ensure long-term durability.
#Step 6: Assembly, Final Checks, and Delivery
The final phase of distribution transformer manufacturing brings together every carefully crafted component to create a product ready for reliable performance. This stage involves precision assembly, thorough inspections, and timely delivery to meet customer expectations.
- Protective Enclosure Assembly: The final assembly process incorporates robust enclosures designed to shield the internal components from environmental damage and operational wear. These enclosures are constructed with materials that withstand harsh conditions, ensuring transformers like electrical power distribution transformers maintain peak performance in industrial environments.
- Final Checks and Quality Validation: Before delivery, each transformer undergoes rigorous inspections to confirm that every aspect of the design, from core assembly to insulation, meets stringent quality standards. These checks validate the transformer’s safety, efficiency, and compatibility with its intended application.
- Efficient Packaging and Delivery: A trusted provider, such as JCL Energy, emphasizes secure packaging to protect the transformer during transit. Our expertise in logistics confirms that the transformer will arrive on time and in optimal condition, ready to integrate into energy systems.
With these meticulous steps, JCL Energy reinforces its reputation for reliability and precision, delivering transformers that meet the unique needs of our clients.
Optimize Your Power Systems with JCL Energy’s Expertise
The process of distribution transformer manufacturing combines technical precision, advanced materials, and rigorous testing to produce transformers built for reliable and efficient energy distribution. Each stage of production, from design to delivery, reflects the expertise and commitment of trusted providers like JCL Energy.
Ready to optimize your energy systems? Connect with JCL Energy today to explore customized solutions designed to meet your power needs. We proudly serve businesses across the United States, Canada, and Mexico with industry-leading products and expert guidance.